Plasma Spray Coating Services
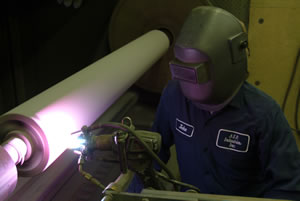
Plasma Electric Arc Ceramic Coating
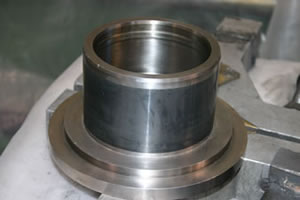
Chrome Oxide Coated Wear Surface
Support Bearing Pullers
What is Plasma Spray Coating?
Plasma Arc spray coatings creates a hard coating surface that protects substrates against wear, oxidation and corrosion wear caused by environmental and operating conditions. The coatings are dense and strong, making plasma spray coating a favorable option for equipment protection and refinishing.
Hannecard – ASB is committed to providing the industry’s best plasma spray coating and other advanced surfacing technology. All equipment is calibrated to ISO standards to optimize your plasma spray coating process. All lot numbers from our powder suppliers are recorded, and, in most cases, sample pieces are processed for testing purposes during production spraying. Documented procedures are recorded for each job, and ongoing inspections are performed for each critical step to ensure consistent coating quality.
Ready to get started? Request a quote or contact our expert team today. We are prepared to provide comprehensive and customized plasma spray coating solutions to improve your operational efficiencies and lower maintenance costs.
The Plasma Spray Coating Process
Plasma spray coatings are applied using a high-temperature process where powdered coating material is injected into a plasma plume. The material is rapidly heated and then accelerated toward the substrate. Once it reaches the surface, it begins to cool, forming a hard coating on the substrate and adding value to your final and finished product, component, or assembly.
Benefits of Plasma Spray Coating
Plasma spray coating processes are highly versatile and create ceramic coatings that can protect components in the most severe environments. Other advantages added by ceramic plasma spray coatings include:
- High Temperature Resistance
- Extreme Wear Resistance
- Inert Chemical Resistance
Common Plasma Spray Materials
The high temperatures involved in plasma spray coating allow the use of ceramics and other materials that have a high melting point. A few of the common materials Hannecard – ASB uses for plasma spray coating processes include:
- Aluminum Oxide
- Chrome Oxide
- Zirconium Oxide
- And others.
Thickness specifications are based on the component application, including wear and corrosion considerations. Along with multilayered coating systems, we will utilize specialized sealing treatments to optimize coating performance. Specialized coating materials may also be available upon request.
Dielectric Shielding Services with Plasma Sprays
If electrical current is an issue, plasma electric arc spray coatings also provide dielectric shielding. Used for an extensive range of industrial applications, these coatings can prevent current from passing through critical components and causing harmful arcing. With the added protection of a plasma spray coating, components are shielded from potentially severe electrical corrosion and damage.
Common Applications of Plasma Spray Coatings
Plasma spray coating is a highly versatile process that is used across many industries, including:
- Aerospace
- Medical
- Marine
- Electronics
- Automotive
- Mechanical Engineering
- Petrochemical
- And many others.
Begin Your Plasma Spray Coating Project with Hannecard - ASB
Submit your project to get our team started on your ceramic plasma coating solution. Contact us for more information, with questions, or to receive additional resources about our plasma spray coating methods.
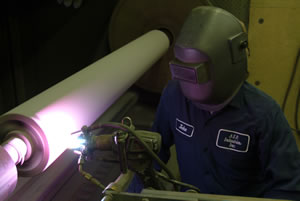
Plasma Electric Arc Ceramic Coating
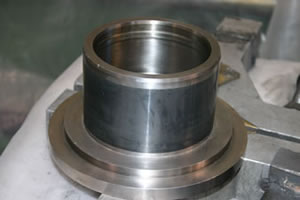
Chrome Oxide Coated Wear Surface
Support Bearing Pullers