Thermal Spray Coatings
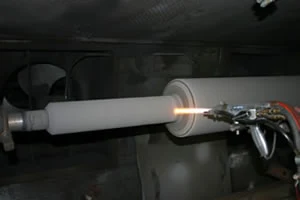
HVOF Thermal Spray Roll Services
Thermal spray processes are a type of surfacing technology used to protect an extensive range of industrial components and equipment. Depending on your project, goals, and selected OEM thermal spray specifications, these coating processes create resistance to wear, corrosion, high temperatures, chemicals, exposed environments, and multiple types of wear. Additionally, thermal spray processing will rebuild worn areas back to OEM dimensions, allowing for component and print assembly.
Thermal Spray Coating Experts
With over 76 years of experience in thermal spray coatings, Hannecard – ASB has the knowledge and understanding to provide superior finished components. Utilizing state-of-the-art equipment and our extensive experience with thermal spray coatings, we can prepare and finish parts while integrating masking, tooling, and fixturing customized to your unique requirements.
Contact us or request a quote to learn more about our thermal spray coatings, including HVOF coatings, plasma spray coatings, and other high-technology thermal spray solutions.
ASB's Industrial Thermal Spray Coatings
Wear Resistance Part Performance Enhancement Coatings
Thermal Spray Coating Processes
Hannecard – ASB has the expertise to apply coatings to nearly any substrate. No thermal spray process is outside our capabilities, enabling us to offer specialized thermal spray coatings that improve equipment performance, boost wear and corrosion resistance, extend component life, and more. Typical thermal spray coating services include:
Plasma Arc Spraying
Plasma Arc spray coatings creates a hard coating surface that protects substrates against wear, oxidation and corrosion wear caused by environmental and operating conditions. The coatings are dense and strong, making plasma spray coating a favorable option for equipment protection and refinishing.
High-Velocity Processes (HVOF Coatings)
The HVOF (High Velocity Oxygen Fuel) coating process combines supersonic particle impact on the substrate with controlled heat energy to produce a consistent hard-particle surface distribution with high bond strengths, low porosity, and high wear resistance.
Electric Wire Arc Spraying
Electric arc results in a spray process that is economically efficient to produce effective results, with very little heat transferred to the workpiece. Additionally, electric arc wire spraying produces spray at higher spray rates than other thermal spray processes, creating some of the fastest coating rates of any coating method.
Cold Spray
With high-pressure cold spray, coating materials aren't melted by a thermal energy source. Instead, energy from high-pressure gas allows injected powder material to reach critical velocity. The cold spray coating process utilizes supersonic nitrogen and/or helium gas jet that propels solid powder particles onto the workpiece at speeds as high as Mach 3 (900 m/s) to create both build up and surfacing layers. As a result, the particles form a strong and dense bond to the substrate.
Combustion Flame Thermal Spray Coatings
Flame spray coating is an all-encompassing term for a number of thermal spray processes. As the name implies, a high-temperature flame transforms the coating materials into a semi-molten state; this molten material is then sprayed onto the workpiece to form a surface coating.
Machining, Grinding, & Finishing Services
Since every thermal/cold spray coating project is unique, Hannecard - ASB develops specific combinations of surfacing technologies and machining procedures to ensure optimal component and equipment performance. Our established in-house procedures and customer-specific quality assurance programs assure that every project meets the required specifications.
All our thermal spray coatings are applied in-house, allowing us to properly prepare workpieces and ensure you only receive the best finished components. On-site thermal spray services are available for certain applications.
What are Thermal Spray Coatings?
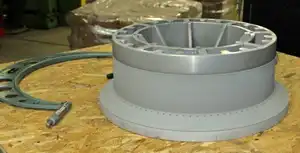
Hard Coated Wire Processing Drum
Thermal spray coatings are a high-technology solution to extend the lifespan of various parts. Encompassing a diverse range of surface engineering technology, thermal spray methods deposit a wide variety of materials onto a substrate to form a coating that protects or enhances the final component. Thermal sprays have been in use for over a century to improve industrial components and structures, offering wear resistance, corrosion resistance, thermal insulation, electrical conductivity, and many other effects.
Thermal Spray Coating Materials
Numerous materials can be used to create thermal spray coatings. Since finding the right coating is crucial, Hannecard - ASB Industries will work with you to determine the best coating material for your needs. We work with metals, alloys, carbides, ceramics, and more to give our customers top quality coatings that deliver the performance and protection their applications require. Some of the materials that we utilize, include:
Metal Coatings
- Aluminum & Aluminum Alloys
- Babbitt
- Carbon Steels
- Copper
- Inconel
- Nickel & Nickel Alloys
- Stainless Steels
- And More
Carbide Coatings
As an ISO 9001:2015 certified company, Hannecard – ASB is prepared to handle the needs of any thermal spray coating application.
What are the Benefits of Thermal Spray Coatings?
Thermal spray coating adds many advantages and benefits to industrial applications across markets. While the exact benefits will vary depending on your selected process, some examples include, but are not limited to:
- Diverse thermal spray methods deliver your required results
- Several applicable materials to fit your specifications
- Improved heat resistance through thermal insulation against excessive loads
- Improved workflow and operations through longer lasting components
- Improved wear resistance, corrosion protection, electrical insulation, and more
What are Applications of Thermal Spray Coatings?
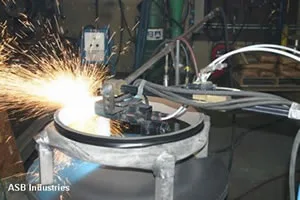
Rebuilding of Mis-Machined Component
Initially developed in the late nineteenth century as a metallizing process, thermal spray methods have evolved over the past century to include other materials and apply to many different substrates. Today, this technology is widely used across industries, including aerospace, automotive, energy, steel, biomedical, and many others. Common thermal spray coating applications include:
- Coating turbine blades to improve wear resistance and extend lifespans
- Applying thermal barrier coatings to gas turbine components for enhanced efficiency
- Depositing biocompatible coatings on medical implants to reduce the risk of rejection
- Custom thermal spray finishes for specialized requirements
- And many more!
Consult With One of Our Thermal Spray Experts
While thermal sprays can serve a multitude of options for many OEMs and manufacturers, sometimes inherent properties are not the best solution for all applications. Certain part shapes and sizes are suitable for thermal spray coating technologies due to achieving optimal coating angles. Many time extreme heat or high forces—which may be a possible option for welding that HRC/ASB can offer. Additionally, some requirements for thick coating which may weaken properties and impact the overall performance of components.
If thermal spray technology is not right for your application, cold spray coatings and other protective surfacing methods are available to match your requirements. Consult with a surfacing technology expert to find your best solution.
Hannecard – ASB: Full-Service Suppliers of Thermal Spray Coatings
Experience, certification, and training are Hannecard – ASB’s greatest assets in providing practical solutions, efficient processes, and on-time deliveries. We have the know-how to provide the industry’s best service to add value to your unique project. Our in-house quality assurance programs guarantee that each thermal spray-coated part is evaluated for coating structure, coating bond, oxide content, porosity, and thickness.
Our certified thermal spray operators and journeyman machinists utilize cutting-edge equipment to make our thermal spray coatings the best in the business. Contact us to learn more about our thermal spray services, processes, and coating technology. Request a quote to receive information specific to your planned application.
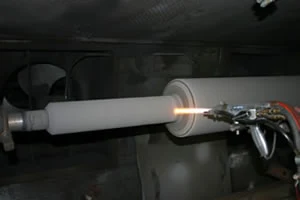
HVOF Thermal Spray Roll Services
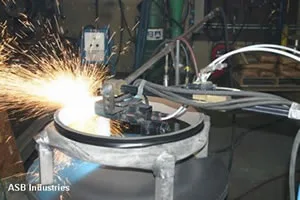
Rebuilding of Mis-Machined Component
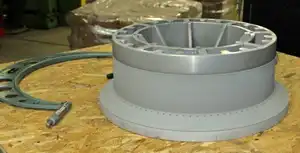
Hard Coated Wire Processing Drum