Wear & Abrasion Resistant Coatings
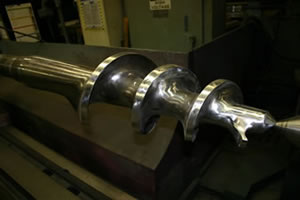
Polymer Injection Screw Carbide Coating for Wear
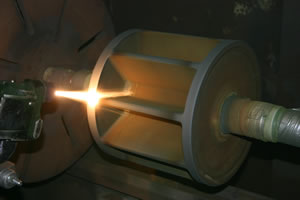
Hard Ceramic Rotor
Abrasion and wear are the most common contributors to industrial component failure. When a component wears out due to constant contact and friction, the result is increased maintenance costs. Hannecard—ASB's thermal spray abrasion-resistant coatings solve that problem. When applied directly to the surface of industrial parts, our wear-resistant coatings protect from abrasion, friction, galling, and seizing, significantly prolonging the life of industrial parts and components.
Thermal Spray Wear-Resistant Coatings from Hannecard - ASB
Hannecard - ASB's abrasion-resistant coatings provide superior protection for industrial parts and equipment, minimizing maintenance requirements and replacement costs by extending the life of components. With our thermal spray capabilities, we can apply abrasion-resistant coatings to nearly any material. We precisely manage the thickness of these coatings, meaning any part can be given added abrasion resistance without sacrificing fit, form, or function.
Benefits of Thermal Spray Abrasion-Resistant Coatings from Hannecard - ASB
- Abrasion Resistance: The coating acts as a barrier, safeguarding equipment from wear and tear caused by friction and contact with abrasive materials.
- Less Maintenance, Lower Costs: By protecting your equipment, the coatings result in less time and money on maintenance and replacements.
- Precision Thickness: We ensure each coating is the optimal thickness for your components.
- Range of Coating Material Options: With multiple high-performance thermal spray coating material options, we provide the proper coating for your unique application.
- In-House Application: We apply our thermal spray coatings in-house, allowing us to manage every step of the process. Everything from initial surface preparation to final grinding and polishing is closely monitored to ensure that your abrasion-resistant coatings meet or exceed your expectations.
Material Options for Thermal Spray Abrasion Resistant Coatings
To a certain extent, all thermal spray coatings improve the substrate material's abrasion resistance. However, Hannecard-ASB works with numerous coating materials specially engineered to provide maximum protection against environmental and operational abrasion. Our certified thermal spray operators use advanced equipment to modify the coating material chemistries and application processes, ensuring your abrasion-resistant coatings are tailored to your specific application's requirements.
Tungsten Carbide Coatings
Tungsten carbide coatings feature superior wear resistance and long-lasting performance. Industries rely on tungsten carbide for its exceptional durability against abrasion and wear. It can also be ground and polished to a specific finish. Tungsten carbide's exceptional resistance to wear and abrasion makes it an ideal solution for a wide range of industrial applications, including roll body and bearing, seal surfaces, heavy machinery components, and more.
Chrome Carbide Coatings
Chrome carbide coatings are favored for their exceptional wear resistance at higher temperatures. While chrome carbide coatings have less wear resistance and hardness than tungsten carbide coatings, their performance at elevated temperatures makes chrome carbide a preferred solution for many high-temperature applications.
Chrome Oxide Coatings
Chrome oxide coatings are ceramic coatings that feature outstanding hardness and density. These high-performance ceramic coatings feature excellent wear, abrasion, and chemical resistance and have an anti-reflective finish. Chrome oxide ceramic coatings are often applied to pump components, rotating equipment, and other parts requiring an increased resistance to wear or chemicals.
Industrial Applications for Thermal Spray Abrasion Resistant Coatings
Hannecard – ASB thermal spray coatings are used in a wide range of industrial applications. Our coatings can be applied to nearly any metal material, as well as certain plastics, ceramics, and composites. They provide superior protection for roll surfaces, pump & valve parts, heavy machinery, and numerous other industrial components. Industrial sectors that directly benefit from abrasion-resistant coatings include:
- Steel
- Paper
- Tissue Converting
- Energy
- Aerospace
- Automotive
- Textiles
- Construction
- OEM
- Military
Secondary Finishing Services & Surface Treatments
We offer machining, grinding, polishing, and surface treatments that will keep your integrated components operating at their peak. Some wear-resistant coatings — tungsten carbide, chrome oxide ceramic, and materials with iron base chemistries — require special grinding media to achieve the proper surface and dimensional finishing requirements. Whether the job requires diamond belts, hard wheels, diamond paste, and/or precision machine tools, Hannecard - ASB has the equipment and the expertise to apply your wear resistance coatings and finish them to your specifications. By incorporating wear resistance coatings in part specifications and design prints, you can greatly improve equipment performance. Documenting these coatings as specifications for future production will help ensure the continued success of your parts and components.
Contact Us for Top-Quality and Innovative Thermal Spray Abrasion Resistant Coatings
Contact us to learn more about our customized abrasion-resistant coating solutions. Or, submit a project to find out what we can do for your application. Our engineers will work with you to determine which coating material and thermal spray process will deliver the most effective abrasion resistance for your application. Hannecard – ASB is your trusted source for industry-leading abrasion-resistant coatings.